Uncovering the Root Cause
Are you focused on the causes
or the symptoms?
The third phase in the DMAIC project lifecycle is ‘Analyze’. This is where we take the data we have collected during the ‘Measure’ phase and turn it into a cohesive story which will then inform how and where we will make improvements. More specifically, we discover the actual Root Cause of the problem we are trying to solve.
Over the past five years we have noticed that ‘data-analytics’ have increasingly become more popular as has ‘data story-telling’. This has been great for marketing the importance of collecting data within organizations however these courses and articles tend to take a broader approach to data (evaluate, clean, summarize) compared to how we analyze data within the DMAIC/Six Sigma framework.
Within Six Sigma, the Analyze activities which take place may include:
- Graphical Analysis (ex. Box Plots, scatter, etc)
- Normality Tests, Distribution ID & Data Transformation
- Process Control Study (control charts)
- Capability Study (Yield, TPY, RTY, DPMO, Z)
- Failure Mode & Effects Analysis (Update RPN)
- Hypothesis Testing, Y=f(x), (Parametric & Non-Parametric)
- Test of Central Tendency (Mean, Median)
- Test of Variance (Dispersion, Standard Deviation)
- Test of Proportion (%)
- Test of Frequency (count, occurrence, Chi-Square)
- Regression Analysis (simple linear, multiple)
- Analysis of Variance (ANOVA & ANOM)
- Validate Findings and Conclusions
- Phase review and approval
As previously mentioned, all of the above listed activities are completed with the objective of finding and validating the Root Cause(s) of the problem and ensuring that any improvement in the next phase is focused on causes rather than symptoms.
Therefore, the first step is to understand the difference between causality and correlation. Causality is the study of how things influence one other, how causes lead to effects (1). Correlation is a statistical measure or connection between two or more things – especially when one influences the other (2). It is important to keep in mind that “correlation does not imply causation” therefore taking sufficient time in your Root Cause Analysis (RCA) is imperative to avoid jumping to conclusions based on observations of correlation.
How do we differentiate between causation and correlation? Some key tools which will aid us in our RCA are:
- 5W2H
- This is an interrogative technique which asks the question ‘Why’ five times and ‘How’ two times to explore the cause of a problem and to expose weaknesses in a system or process. Each ‘Why’ generally forms the basis of the next ‘Why’ question to encourage the team to dig deeper into the problem.
- Failure Mode and Effects Analysis (FMEA)
- This tool is to recognize and evaluate the potential failure of a product or process, the effects of each failure, and to identify actions that could eliminate or reduce the risk of failure as well as document the process.
- Fault Tree Analysis (FTA)
- This is a visualization tool which provides a convenient, symbolic representation of the combination of events that result in a specific outcome or top event. These events or gates are represented by symbols, similar to those in flow charts and follow a binary logic structure of ‘AND/OR’ branch points. In the FTA, the entire system as well as human interactions are analyzed.
- Fishbone Diagram
- This is a visualization tool for identifying and categorizing many potential causes of a problem.
- Pareto Charts
- Commonly referred to as the ‘80/20 Rule’, it is a chart to help identify the vital few from the trivial many and it illustrates dominant ‘before and after’ results.
- Scatter Plot Diagram (aka Dispersion Diagram)
- This is a diagram which illustrates a summary of two sets of data/variables. The Y axis represents the dependent variable and the X axis represents the independent variable. This diagram shows the relationship between the two data sets/variables and aids in the interpretation of the correlation coefficient or regression model.
One observation we have had after reviewing hundreds of projects over the years is that the Root Cause is often smaller and simpler than originally anticipated at the beginning of the project. This has reinforced our conviction that it is very important to not rush through the Analyze phase, to take the time to use the tools listed above so that you are confident that you have identified the actual root cause. Once this has happened you are ready to take action and move to the next phase of your project which is ‘Improve’.
If you have any questions about the tools listed above or would like a refresher on how to use them, please contact us at info@ezsigmagroup.com.
1. https://www.newscientist.com/definition/causality/
2. https://www.jmp.com/en_ca/statistics-knowledge-portal/what-is-correlation.html
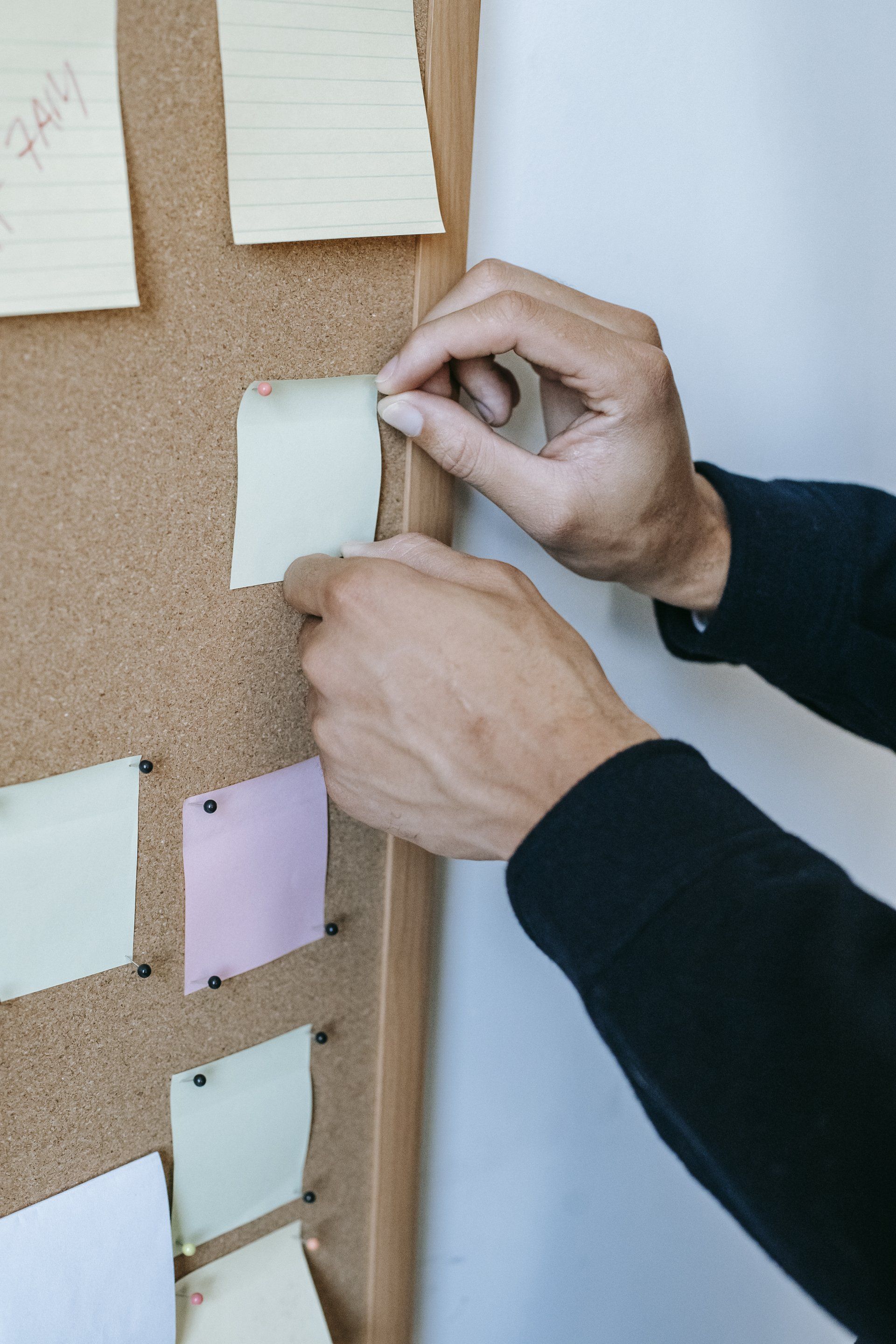